Annual HVAC Operating Costs for New England Commercial Buildings
May 12th, 2025
4 min read
By Dennis Allen
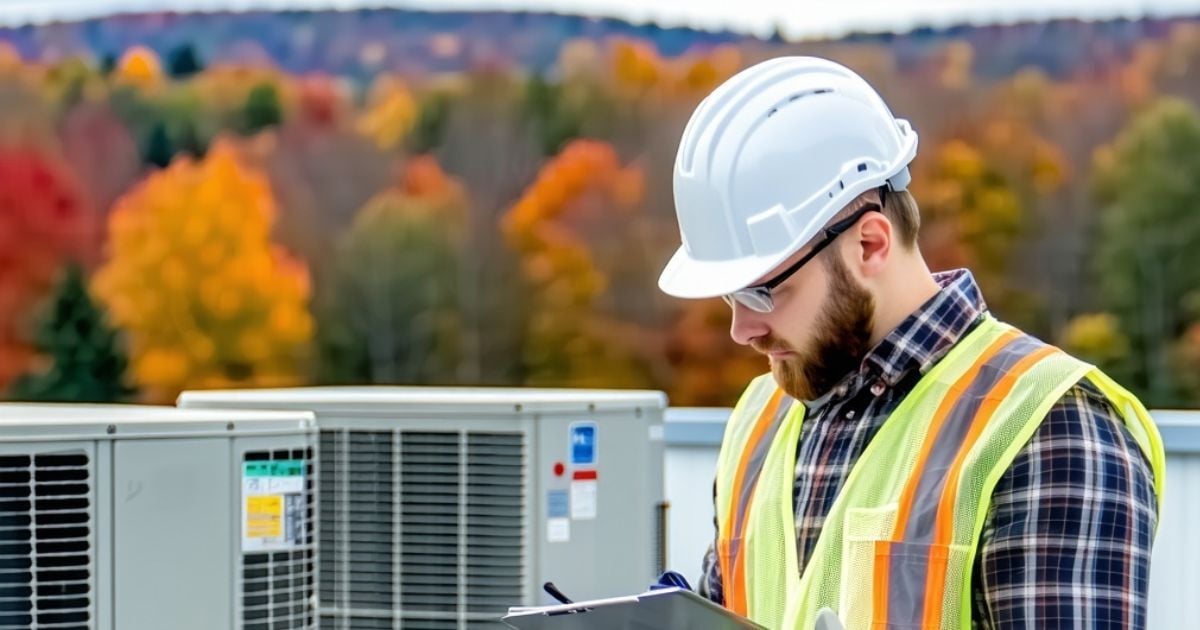
When budgeting for a new commercial HVAC system, the first question most facility managers ask is: “What’s this going to cost me up front?” But the better question is: “What’s it going to cost me every year?”
New England’s weather extremes push your HVAC system to the limit—ice-cold winters, sticky summers, and rapid shifts in temperature all year long. Over time, energy bills, maintenance costs, and surprise repairs can quietly eat into your bottom line.
At Harold Brothers Mechanical Contractors, we’ve been installing and servicing commercial HVAC systems across New England for over 16 years. We’ve seen how real-world costs add up after year one, and we’ve helped hundreds of facility managers reduce them through smart planning, preventive care, and efficient upgrades. Our team knows what those systems really cost to run, and more importantly, how to save.
Read on to learn what typically contributes to the yearly cost of running a commercial HVAC system, everything from energy use and maintenance to repairs and equipment lifespan. We’ll share real-world cost examples from New England businesses, including schools, office buildings, and industrial facilities, so you can see how it plays out in practice. You’ll also gain insight into the key factors that increase or reduce these costs and walk away with practical steps to lower your long-term HVAC expenses.
What Makes Up the Yearly Operating Cost of a Commercial HVAC System
The biggest ongoing HVAC expense for most buildings is energy. Commercial HVAC systems run constantly to maintain comfort. Depending on your building’s size and usage, utility bills can be substantial.
According to the U.S. Energy Information Administration, U.S. commercial buildings spend more than $140 billion annually on energy, and New England ranks among the highest in energy cost per square foot.
Maintenance is another major factor. Tasks like changing filters, cleaning coils, and inspecting electrical components help your system run more efficiently and reduce energy consumption. They also prevent costly problems down the road.
Read more about the importance of preventive maintenance to learn what proactive care can include and how it protects your investment.
Even well-maintained systems will eventually face wear and tear. Motors, belts, and sensors break over time—especially during peak heating and cooling seasons. Emergency repairs after hours can easily double in cost. That’s why many facility managers opt for service contracts with benefits like priority scheduling and discounted repair rates.
Typical Annual HVAC Costs for Commercial Buildings in New England
Every facility is different, but after almost two decades in the field, we’ve seen some clear patterns emerge. Here’s what annual HVAC costs might look like across three common building types in New England:
Building Type |
Energy |
Maintenance |
Repairs |
Estimated Total |
Small Office (5,000 sq ft) |
$5,000–$15,000 |
$1,000 - $5,000 |
$500 - $5,000 |
$6,500 – $25,000 |
School (50,000 sq ft) |
$50,000 – $120,000 |
$5,000 - $25,000 |
$2,500 - $10,000 |
$57,500 – $155,000 |
Industrial Facility (100k+) |
$100,000+ |
$20,000+ |
$5,000+ |
$125,000+ |
These figures are based on real-world examples from our clients across the region. Usage schedules, utility rates, and equipment efficiency all play a role in shaping your specific numbers.
Top Factors That Increase or Reduce Commercial HVAC Costs
New England’s climate is one of the biggest cost drivers. Your HVAC system is likely running during every season, switching between heating, cooling, and ventilation. Add to that Massachusetts’ high utility rates, and energy becomes a critical budget factor.
System age is another major influence. Older units typically consume more power and break down more often, which adds repair costs and shortens equipment lifespan. Similarly, facilities that operate 24/7, like hospitals or data centers, put more strain on their systems, accelerating wear and increasing costs.
On the other hand, buildings that invest in energy-efficient equipment and use smart controls like programmable thermostats or building management systems often see their annual HVAC costs decline. These systems can adjust automatically to occupancy levels, time of day, and even outside temperatures, trimming energy use without sacrificing comfort.
Regular maintenance is where long-term savings are most obvious. When filters are changed on schedule, components are cleaned, and worn parts are replaced early, the system runs smoother and lasts longer. Think of it like taking care of your car—a little attention now avoids a major repair later.
Proven Ways to Cut Commercial HVAC Costs Year Over Year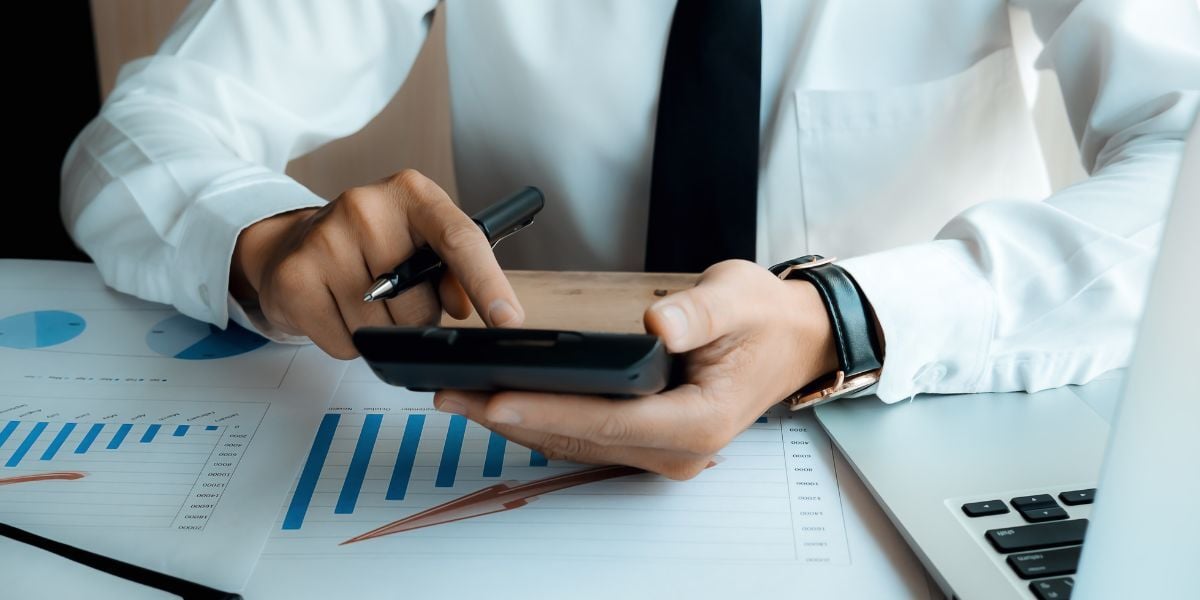
1. Upgrade to High-Efficiency Equipment
Modern HVAC systems are designed for performance and savings. Look for units with high SEER ratings and ENERGY STAR certification to lower your monthly utility bills.
2. Add Smart Controls and Monitoring Tools
Smart thermostats, sensors, and building management systems improve comfort while reducing energy use, especially during off-hours or seasonal transitions.
3. Commit to Preventive Maintenance
Don’t wait for a problem to surface. A well-structured service agreement extends system life, improves reliability, and avoids costly reactive service calls.
4. Use Energy Audits and Retro-Commissioning
Fine-tune your system every few years. You may uncover duct leaks, outdated settings, or opportunities for automation that save thousands annually.
Bonus: Some upgrades may qualify for federal deductions under IRS Section 179D.
Get Ahead of Commercial HVAC Costs With a Proactive Strategy
HVAC costs are predictable when you plan for them. With the right equipment, proactive service, and energy-smart strategies in place, you can avoid most of the surprises that cause budgets to balloon.
At Harold Brothers, we help businesses across New England build sustainable HVAC strategies that align with their operations and budgets. Whether you manage a small office, a school campus, or a sprawling industrial facility, our team is here to help you reduce downtime, lower energy use, and extend the life of your system.
If you want to get ahead of your HVAC costs, the first step is understanding where you stand. Read our Preventive Maintenance Walkthrough to see what a well-structured service plan includes and how it helps you avoid unexpected expenses throughout the year.
Harold Brothers Mechanical Contractors has helped businesses across Massachusetts and New England control their HVAC costs for over 16 years. Whether you operate a school, office, healthcare facility, or manufacturing plant, we’re here to help you save more and stress less.
Dennis Allen is the COO and Director of HVAC at Harold Brothers Mechanical. With over 20 years in the trade, he leads the HVAC division and mentors the next generation of technicians. A board member for the Massachusetts Pipefitters and Refrigeration Board, Dennis is passionate about education, field excellence, and emerging technologies like VRF systems.
Topics: