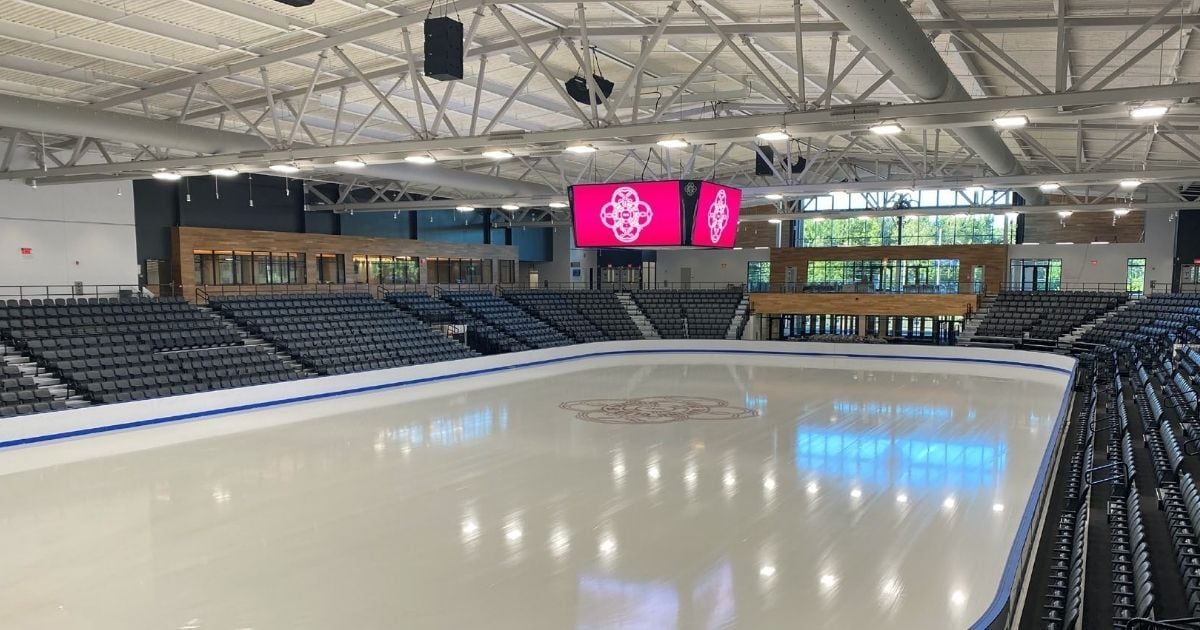
Challenge #3: HVAC Zoning and Airflow in Stadiums
The Problem:
A stadium is made up of many different areas. These include locker rooms, restrooms, kitchens, luxury suites, concession stands, concourses, and seating areas. Some places need climate control even when the stadium is empty. Others only need it during events. The number of people in the building can go from a few hundred to tens of thousands, depending on the day.
The Fix:
This is where zoning comes in. Modern HVAC systems can be split into zones that serve different parts of the stadium independently. Variable Air Volume (VAV) systems let you control how much air goes where, based on what’s needed.
With smart controls and sensors, the system can respond in real time to occupancy changes. This keeps fans and staff comfortable without wasting energy. For best results, follow zoning and airflow design standards such as those provided by ASHRAE.
Challenge #4: Protecting Indoor Air Quality During HVAC Replacement
The Problem:
During HVAC replacement, workers may need to open ducts, drill through walls, or remove old units, all of which can create dust and debris. If that dust makes its way into public areas, kitchens, or health facilities (like training rooms), it could be a major safety concern.
Without the right containment, construction dust and fumes can affect air quality in kitchens, locker rooms, and training spaces, which is why the EPA’s indoor air quality guidelines are especially important during major renovations. Poor air quality also puts your building at risk for failed inspections or fines.
The Fix:
Set up clean, contained work zones. Use plastic barriers or temporary walls to block off construction areas. Contractors should use HEPA-filtered tools and vacuum systems to reduce airborne particles. Portable air purifiers or fans may also help direct clean air where it is needed. Before the system is turned on, schedule an air quality test to confirm the space is safe for use. Following indoor air quality guidelines from the EPA can help keep your building compliant and healthy.
Challenge #5: Budget Overruns and Scope Creep in Stadium HVAC Work
The Problem:
It is common for stadium HVAC projects to grow in size after work begins. You might start with rooftop units, only to find outdated controls, worn-out ductwork, or poor insulation. Each surprise adds more time and more money to the project.
The Fix:
The best way to avoid budget shocks is to expect them. Build a contingency into your project estimate from the start. Instead of just adding 10–20% for surprises, fund allocation should be based on a thorough lifecycle cost.
Before any physical work begins, ask for a full system assessment including the electrical, structural, and ductwork components. This helps you spot hidden issues before they become expensive surprises. Prioritize what’s most critical, and plan for future upgrades in phases if needed.
After project completion, don’t wait until something goes wrong—check out our best practices on commercial spring HVAC preparation to keep airflows clean, systems efficient, and energy costs down.
How to Successfully Plan and Execute a Stadium HVAC Upgrade
Replacing an HVAC system in a stadium is a major project, but it can be done safely and efficiently with the right plan. You will improve comfort, indoor air quality, and energy use for years to come.
The biggest risks are usually related to time, access, airflow, air quality, and budget. Each of these challenges can be managed with the right team and strategy.
If you're preparing for HVAC work in an active stadium or public venue, your biggest concern might be keeping your doors open. Our guide on staying open during HVAC repairs explains how to do just that.
At Harold Brothers, we’ve helped some of New England’s most complex stadiums and other commercial facilities upgrade their HVAC systems safely and efficiently. Whether you’re upgrading rooftop units or redesigning your entire system, our team can help you plan it right from day one.
Topics: